2Integrating technology with hard work.
Koyaguchi Pile
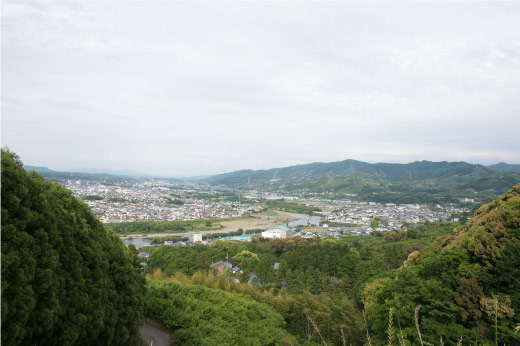
Koyaguchi-cho, in Hashimoto city, Wakayama Prefecture, sits at the foot of Mt. Koya. The Kinokawa river flows through it; in the fall, the area blooms thick with persimmons. Koyaguchi Pile Fabric, with its thick, varied texture, has been made here for generations, taking on all kinds of different styles and forms. To learn more about it, we sat down with Shoji Taenaka, managing director of Taenaka Pile Fabric.
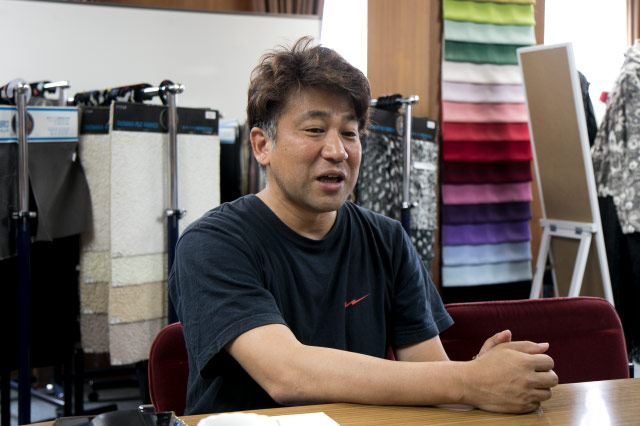
Shoji Taenaka, the managing director of Taenaka Pile Fabric.
- ――
- Thank you for meeting with us today. Let’s get right to it: What is pile fabric?
- Taenaka
-
“Pile” refers to the threads protruding from the surface of a fabric. So when a woven or knit textile is made so that threads or hairs stick out from the surface, it’s called pile fabric.
When we say pile, most people think of the way the loops stick out from the surface of a towel. But we don’t make towels in Koyaguchi. We make things like faux fur and moquette, which is the kind of fabric you see on train upholstery, as well as velvet that’s used for curtains and apparel.
- ――
- So it’s fuzzy and feels good to touch. It also feels luxurious.
- Taenaka
- Some fabrics, like corduroy and velveteen, feel similar to what we make, but the process is different. Those are made by weaving weft yarn into a normal textile and then cutting and brushing the threads to give it a fuzzy texture.
- ――
- How long has this area been making pile fabric?
- Taenaka
-
There used to be a large cotton industry here. Because the Kinokawa River is nearby, if you dig seven to eight meters into the ground you’ll find water. That attracted a lot of dyeing factories, which led to the production of fabrics and dyes.
In the Edo period (1603 - 1868), a fabric called Kawakami Nell was created here. Nell is like a normal cotton fabric, except thistle fruit was used to create pile by pulling the threads up off the surface. The written record says that this fabric was first offered to the feudal lords in the Kishu domain, in present-day Wakayama.

- ――
- An abundant source of water must be crucial for producing fabric.
- Taenaka
-
That’s right — many phases of production use it.
In the Taisho era (1912 - 1926), rewoven fabrics were made in this area. This type of fabric was originally produced in Czechoslovakia, but it was independently invented here. For example, do you know Feiler handkerchiefs?
- ――
- Yes — they’re high-quality hand towels with bright, floral designs.
- Taenaka
- That’s right. Those are rewoven fabrics. First, the warp (vertical) threads of a woven textile are cut. That’s spun into chenille yarn, which is then used as the weft (horizontal) threads and woven together again. The pattern is planned out beforehand; in order for the pattern to come out right during the second weaving, one must be very particular in weaving the fabric the first time. Our company doesn’t produce rewoven fabric, but it’s still made in this area.
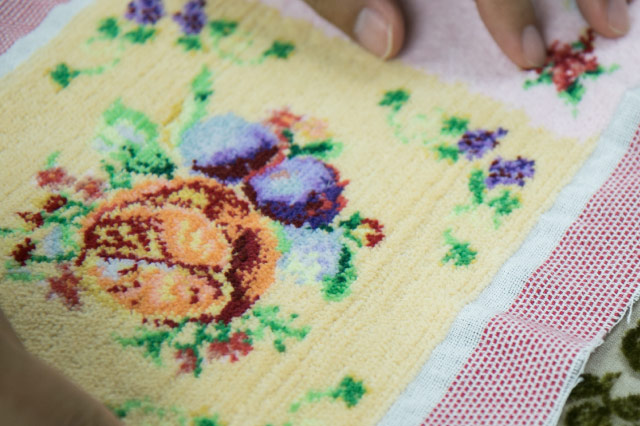
Rewoven fabric. It’s incredibly laborious, but the exact same pattern is produced on the opposite side.
- ――
- So ever since the Edo period, this region has explored the possibilities of pile fabric.
- Taenaka
- That’s true. Velvet and moquette were first woven here before the war. Those are made by weaving two normal fabrics together.
- ――
- What does that mean?
- Taenaka
- So, normal fabrics are made with vertical and horizontal threads.
- ――
- Right.
- Taenaka
- Now take two pieces of this normal fabric and weave them together. A separate warp thread goes through the weft threads of each fabric. Those warp threads holding together the two pieces are cut, creating two tufted surfaces.
The cutter of a loom. As the cutter goes back and forth it cuts the fabric in two and is sharpened by the circular whetstone.
- ――
- Wow! So threads are woven through two pieces of fabric, and when they’re cut apart, that makes the pile?
- Taenaka
- Right! What was the interior of the fabric becomes the exterior. A long time ago, the process involved taking a normal fabric, passing a third thread through it, and weaving loops into it. A craftsman would cut every loop by hand to make the pile.
- ――
- Wow, that’s really involved.
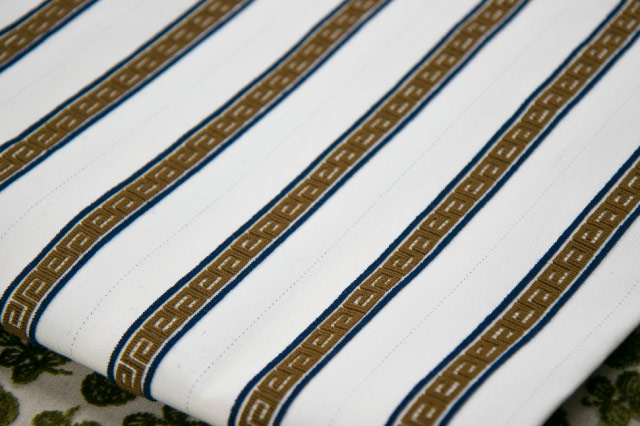
A modern reproduction of the hand-produced trimming used to upholster the imperial carriage. It’s reupholstered every 20 years.
- Taenaka
- It really is. People knew just how difficult it was to produce, so they figured they might as well try improving the process by sewing two fabrics together and cutting them apart. That’s when machines developed in Germany were introduced to the area.
- ――
- Is that how this year’s Hobonichi Techo cover “Japanese Fabric - Hanajutan” was made?
- Taenaka
- Yes. Here we make everything from the yarn to the cloth. We used to dye the thread as well, but we had to stop recently when demand dried up. We started out making pile fabric for clothing. There was a time after that when our main products were faux fur and moquette for jackets. We even made blankets for a while. We’ve also made seat upholstery for the 700-series Shinkansen and the Hankyu train line. At one point, over 80 percent of our sales were for car seats, but today we barely sell any of that.

Seats on the 700 series Shinkansen. The pattern is woven with complicated threads before a print is applied to the surface.
- ――
- It sounds like the uses for pile fabric have really changed with the times.
- Taenaka
- That’s one way to put it. You could also say that it’s being phased out all over as time goes on. Right now we make cleaning cloths for LCD screens.
- ――
- Is pile fabric used in manufacturing processes?
- Taenaka
- Yes. It’s used on iPhone panels during manufacture. That’s 30 percent of the world’s market.
- ――
- Wow.
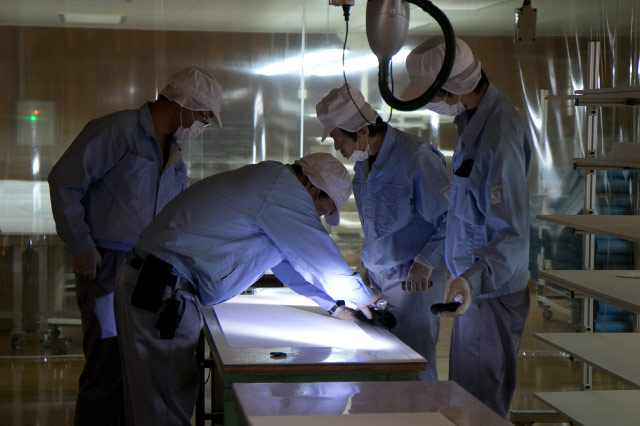
Inspecting cleaning cloths is incredibly detail-intensive work.
- Taenaka
- That has breathed some life back into our business, but we’re still at an eighth of the sales we had back when we were making car upholstery. And apparently the new iPhone doesn’t need our cloth anymore! (laughs) So it’s time to start over again. Right now we’re trying out several kinds of material for a new type of powder puff.
- ――
- That sounds like hard work.

Various pile fabrics. Some are recreations of patterns from over a century ago.
- Taenaka
- Producing a wide variety of smaller lots has become much more common for us — it happens all the time. We’ll have European designers bring us old fabric and ask us to recreate it.
- ――
- And are you able to recreate it?
- Taenaka
- Usually we are. We even matched the chairs in the Diet. When the Democratic Party took power, they came to us and said, "Make the same thing as before.”
- ――
- So when the ruling party changes, the seats get reupholstered?
- Taenaka
- It did this time, at least.

This upholstery for the seats in the Diet was recreated based on an existing sample.
- ――
- How was the Japanese Fabric - Hanajutan techo cover made?
- Taenaka
- There’s a place here that creates paper patterns for pile fabric designs. I shrunk their design down to fit the techo.
- ――
- Was that a simple task?
- Taenaka
- There’s a lot of detail, so simply shrinking it wouldn’t have reproduced it faithfully. We had the company rearrange the pattern to fit onto the smaller canvas. The warp yarn is hemp, and the weft yarn is cotton.
- ――
- So that’s what makes this cover look so unique.
- Taenaka
- This cover wasn’t made by weaving dyed threads together; it was woven in white and then dyed later. If you make the base and the pile out of different materials, you can dye each one separately. So the pile is made of acrylic yarn.
- ――
- That’s amazing!

The white fabric before dyeing.
- Taenaka
- The base was very white, so the pile was dyed after the base, with a special dye. So technically the fabric was dyed twice.
- ――
- There isn’t a single easy part of this process, is there?
- Taenaka
- Very few places in the world can still weave pile fabric. Sometimes people come from overseas to tour our factory, but just buying the same machines we use is no guarantee of good results. We never use a loom as-is; each machine is customized extensively to accommodate the fabric. They do the weaving, that’s only the beginning. We’re proud of how difficult it is to replicate our work.


It takes time to set the warp threads, but when preparing to weave pile fabric with a pattern, it’s also necessary to set the threads for the pile.
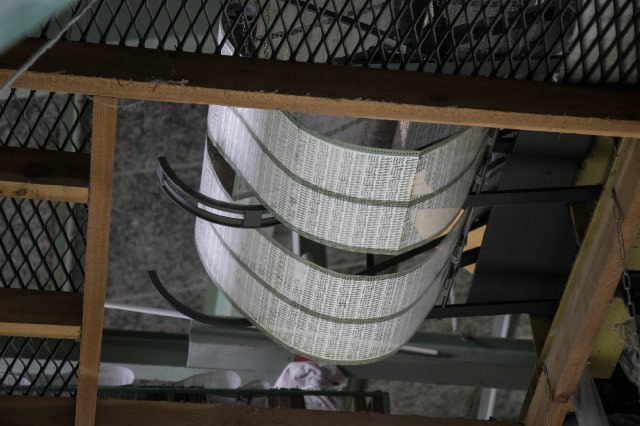
A template set onto a loom. The pattern changes depending on the shape and size of the holes.
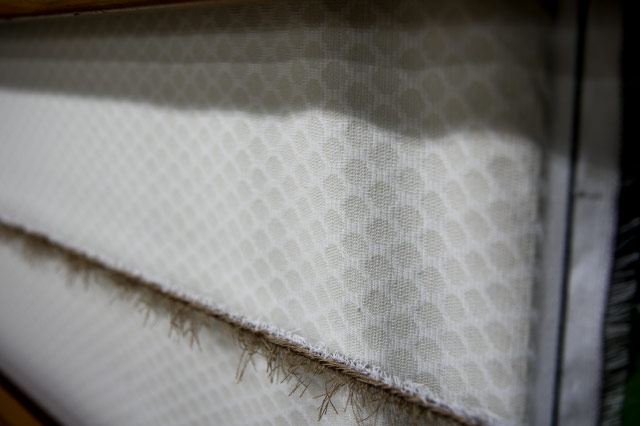
The fabrics are set to face one another and woven on the inside.

Fabric that’s been cut.
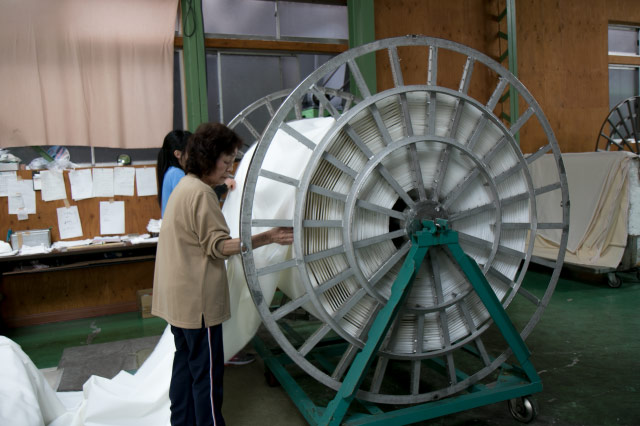
The cloth is dyed by hand after wrapping it up in a frame

A board used to print on fabric.
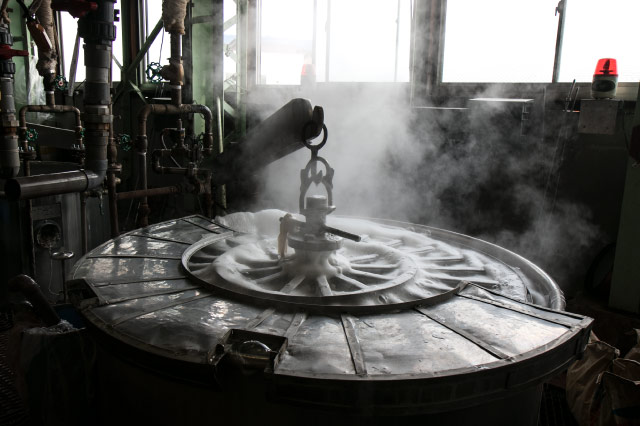
During the dyeing process, the rolled-up cloth pictured earlier is dipped, frame and all, into the dye.
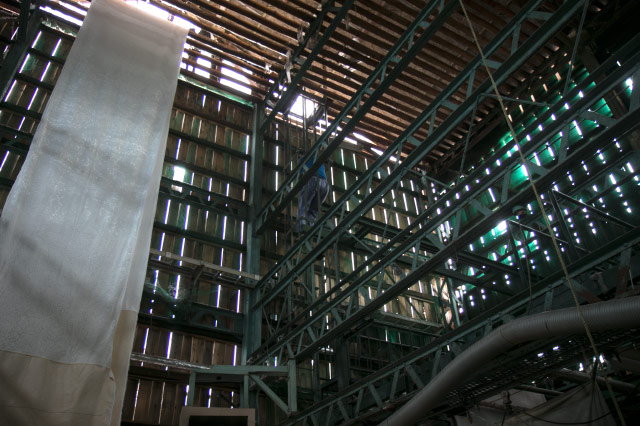
Drying the cloth. Some materials must be air-dried in a drying room with good ventilation. The cloth is hung up by hand.

The brushing process. The pile is set with a brush, and extra length protruding from the surface is trimmed down.

Rolling up and shipping finished cloth. To prevent wrinkles and ensure the pile is not flattened during shipment, the cloth requires extra care during packaging.
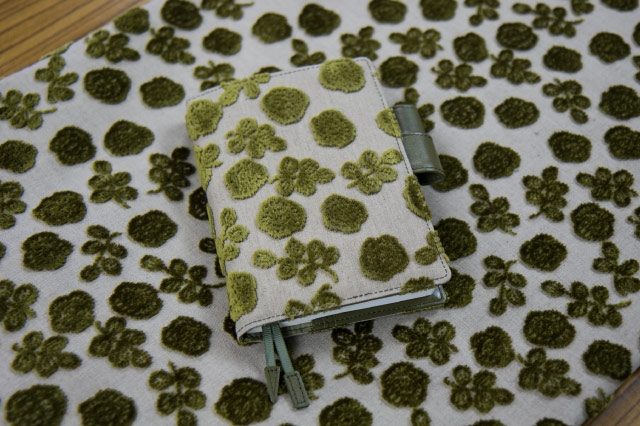
Finished fabric that’s gone through the many stages of Koyaguchi Pile Fabric manufacture.